Quality control in additive manufacturing represents a fascinating intersection of technological innovation and meticulous craftsmanship. It stands as a testament to our ability to harness the boundless potential of 3D printing while maintaining unwavering standards of excellence. Yet, beneath the surface of this revolutionary process lies a labyrinth of complexities and challenges that demand our utmost attention and ingenuity.

At the core of effective quality control in additive manufacturing lies the art of process monitoring. This entails a meticulous examination of key parameters such as temperature, laser power, and deposition rate in real-time. By employing advanced technologies like high-speed cameras and infrared thermography, manufacturers gain unprecedented insight into the dynamic interplay of materials, enabling them to make timely adjustments and interventions to ensure optimal printing conditions.
However, the journey towards quality excellence does not end with process monitoring alone. Rigorous inspection is equally essential, serving as the proverbial checkpoint where the integrity of each printed part is scrutinized with unwavering precision. Non-destructive testing methods like X-ray scanning and ultrasonic testing play a pivotal role in this process, allowing manufacturers to uncover hidden defects without compromising the structural integrity of the component. Complementing these techniques are destructive testing methods such as metallography and mechanical testing, which provide a deeper understanding of material properties and performance characteristics.
Yet, the pursuit of quality in additive manufacturing extends beyond the confines of the production floor. It requires a steadfast commitment to adherence to stringent standards and certifications that serve as pillars of excellence in a rapidly evolving landscape. Organizations like ASTM International and ISO offer invaluable guidelines for quality management systems, providing manufacturers with a roadmap towards achieving and maintaining the highest standards of quality and reliability. Furthermore, industry-specific regulations from entities such as the FAA and FDA set the bar for safety and performance in critical sectors like aerospace and healthcare, ensuring that additive manufacturing technologies are deployed responsibly and ethically.
Looking towards the horizon, the future of quality control in additive manufacturing holds promise and possibility. Emerging technologies such as artificial intelligence and machine learning offer tantalizing prospects for predictive quality control, enabling manufacturers to anticipate and mitigate potential defects before they arise. Likewise, advancements in in-situ monitoring and the development of digital twins promise to revolutionize the way we approach quality assurance, ushering in an era of virtual testing and simulation that transcends the limitations of traditional inspection methods.
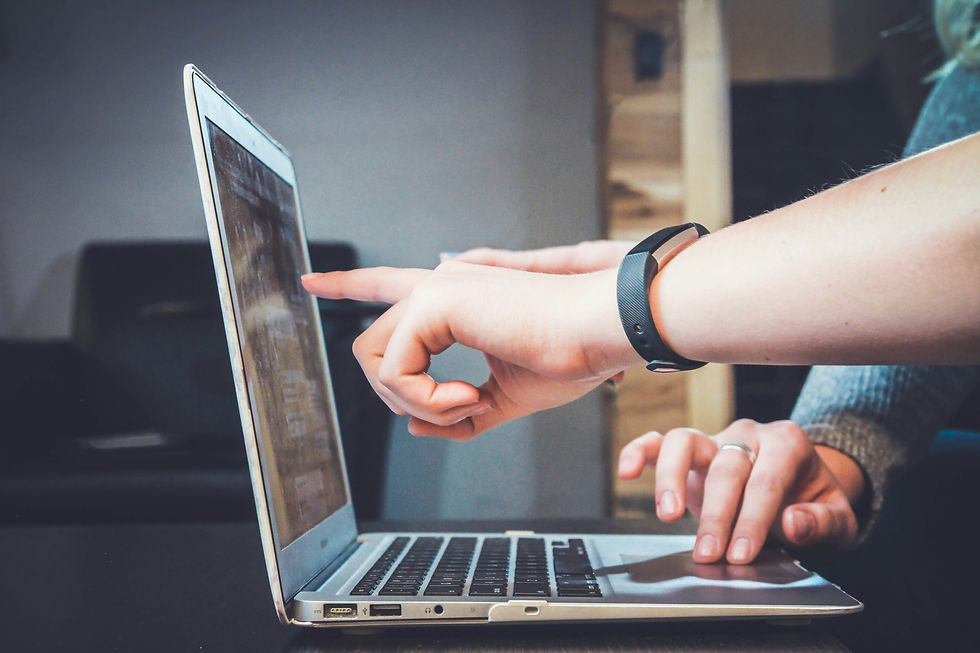
In essence, quality control in additive manufacturing is not merely a box to be checked or a hurdle to be overcome; it is a journey of continuous improvement and innovation. By embracing the complexities of the process, leveraging the power of advanced monitoring and inspection techniques, and adhering unwaveringly to the highest standards of excellence, we pave the way for a future where additive manufacturing stands as a beacon of reliability, efficiency, and ingenuity.
Comments